使用硅作為陽極的全固態(tài)電池在沒有固電解質(zhì)界面(SEI)持續(xù)增長的情況下表現(xiàn)出了良好的性能。然而,第一周期的不可逆容量損失導(dǎo)致硅的初始庫侖效率(ICE)較低,從而限制了能量密度。
為了解決這個(gè)問題,近日,加利福尼亞大學(xué)圣迭戈分校Ying ShirleyMeng、Jihyun Jang團(tuán)隊(duì)采用了預(yù)鋰化策略來提高全固態(tài)硅電池的內(nèi)切效率和電導(dǎo)率。研究人員觀察到,與鋰鈷氧化物(LCO)陰極配對的 Li1Si 陽極的 ICE 有明顯提高。此外,與鎳錳鈷氧化物(NCM)鋰電池的比較顯示,通過硅預(yù)鋰化提高性能僅適用于以高陽極不可逆性為主的全電池。采用這種預(yù)鋰化策略,與純硅相比,1000 個(gè)循環(huán)后的容量保持率提高了 15%。對于 Li1Si,使用干法 LCO 陰極薄膜可實(shí)現(xiàn)高達(dá) 10 mAh cm-2 的高電容,這表明預(yù)鋰化法可能適用于高負(fù)載的下一代全固態(tài)電池。
【背景】
幾十年來,人們一直在廣泛研究鋰離子電池 (LIB) 中的硅。許多報(bào)告指出,由于純硅與液態(tài)電解質(zhì)的界面穩(wěn)定性差,且在循環(huán)過程中會粉化,因此使用純硅作為負(fù)極是不切實(shí)際的。然而,最近的一項(xiàng)研究表明,使用重量百分比為 99.9% 的微硅(μSi)陽極與硫銀鍺礦固體電解質(zhì)(Li6PS5Cl)相結(jié)合,可以生產(chǎn)出具有高平均電流密度和高平均負(fù)載的 ASSB。成功使用 μSi 作為陽極的原因在于硫化物電解質(zhì)-硅界面的鈍化,限制了導(dǎo)電性差的固體-電解質(zhì)界面(SEI)的生長。
雖然已證實(shí)硅基全固態(tài)電池具有鈍化 SEI 和高能量密度,但還可以進(jìn)一步提高性能,包括提高初始庫侖效率 (ICE)、電子電導(dǎo)率和 Li+ 擴(kuò)散率(圖 1)。值得注意的是,傳統(tǒng)上在 LIB 中采用的硅預(yù)鋰化可能是實(shí)現(xiàn)這種改進(jìn)的好方法。
圖 1:用于全固態(tài)電池的硅和預(yù)石墨化硅的比較。硅(淺藍(lán)色陰影)和預(yù)硫化硅(綠色陰影)陽極在各種電化學(xué)特性和電池性能指標(biāo)方面的雷達(dá)對比圖。
電化學(xué)預(yù)鋰化是成熟的預(yù)鋰化方法之一。在這種方法中,通過構(gòu)建一個(gè)由鋰金屬對電極和非水系電解質(zhì)組成的電化學(xué)電池,對硅電極進(jìn)行鋰化。兩個(gè)電極的氧化還原電位差會導(dǎo)致硅的自發(fā)鋰化和 SEI 的形成。然而,"電化學(xué) "預(yù)鋰化的程度必須得到很好的控制,因?yàn)殇嚮蛔銜?dǎo)致鋰捕獲位點(diǎn)殘留,從而無法改善 ICE,而鋰化過度則會導(dǎo)致陽極表面開始析鋰。由于鋰具有很高的化學(xué)反應(yīng)活性,成功實(shí)施預(yù)鋰化的挑戰(zhàn)之一在于找到穩(wěn)定的預(yù)鋰化試劑(鋰源)。因此,Cao 等人引入了一種聚合物來保護(hù)鋰源,將用于預(yù)鋰化的金屬鋰源在制成全電池之前由聚合物屏蔽。更具有商業(yè)可行性的預(yù)鋰化試劑是穩(wěn)定金屬鋰粉(SLMP)。Ai 等人開發(fā)了一種在負(fù)極材料上涂覆 SLMP 的溶液工藝,在對負(fù)極進(jìn)行預(yù)鋰化處理后,石墨/NMC 和 SiO/NMC 全電池的 ICE 值均提高了 31%。Forney 等人將 SLMP 沉積在硅-碳納米管(CNT)陽極上,并使用機(jī)械壓力機(jī)對疊層施加 100-300 PSI 的壓力,持續(xù) 30-60 秒,使 SLMP 的電子絕緣 Li2CO3 涂層破裂,從而促進(jìn)預(yù)鋰化過程。另一項(xiàng)研究表明,鈍化鋰金屬粉末(PLMP)與硅/石墨電極之間的接觸就能誘導(dǎo)預(yù)鋰化。
最近有報(bào)道首次在硅基全固態(tài)電池中使用了硅陽極預(yù)鋰化技術(shù),通過在無水正己烷中加入金屬鋰進(jìn)行球磨來完成硅的預(yù)鋰化。從預(yù)鋰化硅開始,需要進(jìn)一步機(jī)械化學(xué)研磨,將 LixSi 活性材料、固體電解質(zhì)和碳添加劑混合在一起,形成復(fù)合陽極。LixSi 復(fù)合電極與硫陰極配對,整個(gè)電池在超過 500 次循環(huán)后仍能保持穩(wěn)定的容量。雖然這種性能令人印象深刻,但這項(xiàng)工作需要在有機(jī)溶劑中進(jìn)行額外的高能球磨步驟,對硅進(jìn)行預(yù)鋰化,從而增加了 ASSB 制造工藝的復(fù)雜性。過去也曾報(bào)道過使用不含電解質(zhì)的 SLMP 進(jìn)行預(yù)鋰化的方法。Jang 等人成功地在液態(tài)電解質(zhì)中實(shí)現(xiàn)了無碳與含氟聚合物配對的硅預(yù)鋰化,以減輕 SEI。Lee 等人在全固態(tài)電池中實(shí)現(xiàn)了 SLMP 誘導(dǎo)的無電解質(zhì)石墨硅預(yù)鋰化。
【工作要點(diǎn)】
本工作介紹了一種在 ASSB 制造過程中用于硅陽極的簡單壓力誘導(dǎo)預(yù)鋰化策略,并使用固態(tài)核磁共振 (ssNMR) 對預(yù)鋰化硅陽極進(jìn)行了表征。研究人員在對稱電池、半電池和全電池中對預(yù)鋰化硅陽極的性能進(jìn)行了評估。在這項(xiàng)工作中,首次根據(jù)陰極選擇和 N/P 比評估了 ASSB 中預(yù)鋰化的有效性。在長期循環(huán)性方面,與 LCO 配對的預(yù)層化硅電池顯示出超過 95% 的高 ICE,在 5 mA cm-2 電流密度下可穩(wěn)定循環(huán) 1000 次。
有趣的是,研究人員發(fā)現(xiàn)陰極的不可逆性決定了預(yù)鋰化對全電池的影響,而高 N/P 比的硅電池在存在過量硅的情況下與液態(tài)電池的表現(xiàn)完全不同。對于固態(tài)電池,硅在其二維界面上部分鋰化,而不是在陽極內(nèi)處于低電荷狀態(tài),其行為始終與 N/P 比為 1 的電池相同。此外,即使預(yù)鋰化硅的負(fù)載高達(dá) 10 mAh cm-2,也能實(shí)現(xiàn)改進(jìn)的 ICE,這表明了硅陽極與高負(fù)載陰極的真正可行性?;谶@種新的認(rèn)識,研究人員的工作為在 ASSB 配置中正確采用預(yù)鋰化硅提供了啟示。
壓力誘導(dǎo)的硅預(yù)鋰化
硅的預(yù)鋰化是通過一個(gè)簡單的混合過程和一個(gè)加壓步驟進(jìn)行的。在這項(xiàng)工作中,首次在 ASSB 中引入了由渦流混合的 μSi 和 SLMP 組成的陽極。將不同量的 SLMP 與 μSi 粉末混合,生產(chǎn)出摩爾比 x = 0.25、1 和 2 的 LixSi 合金(如 Li0.25Si、Li1Si 和 Li2Si)。研究人員注意到,這些 x 值假定 μSi 粉末中的 SLMP 已完全反應(yīng)。掃描電子顯微鏡(SEM)對 μSi 和 SLMP 的形態(tài)進(jìn)行了研究,結(jié)果表明 μSi 的粒度分布為 2-5 μm,球形 SLMP 的粒度分布為 10-60 μm。從圖 2a 中研究人員發(fā)現(xiàn),最終 Li1Si 粉末中的硅和鋰疇保留了前驅(qū)體顆粒的形態(tài)。由于鋰 X 射線轉(zhuǎn)變的能量較低,Li1Si 粉末樣品中的球形區(qū)域沒有能量色散 X 射線圖譜(EDS)信號,因此可將其歸類為純金屬鋰(圖 2a)。圖 2b 是 200 MPa壓制的 Li1Si 粒子的截面聚焦離子束掃描電子顯微鏡(FIB-SEM)圖像。壓制的 Li1Si 樣品呈現(xiàn)出兩種類型的疇:1) 由不同的 μSi 和 Li 子域組成的區(qū)域,以及 2) μSi 和 Li 前體合金化形成新化學(xué)成分的區(qū)域。在第一類區(qū)域中,鋰子域夾在μSi 域之間,形成了與 SLMP 前驅(qū)體粉末不同的形態(tài)。同樣,也無法從這些富含鋰的子域中檢測到 EDS 信號。第二類疇的形態(tài)與原始μSi和SLMP粉末完全不同,更類似于帶電(鋰化)硅,在這種情況下,單個(gè)硅粒子之間的間隙消失,取而代之的是大硅塊的形成。此外,還可以從這些區(qū)域檢測到硅 EDS 信號。這些分析表明,在 200 MPa加壓 30 秒后,Li1Si 陽極顯示出未反應(yīng)的 Li 和 μSi 以及 Li-Si 合金相。在壓力誘導(dǎo)的鋰化過程中,硅通過鋰的擴(kuò)散而被鋰化,在鋰和硅的接觸點(diǎn),鋰的擴(kuò)散遵循菲克第二定律。然而,在低壓下壓制鋰和硅混合物時(shí),鋰和硅顆粒的接觸面積是有限的。
圖 2:壓力誘導(dǎo)硅鋰化的形態(tài)和核磁共振波譜。a 循環(huán)前未壓制(0 MPa,0 秒)和 b 壓制(200 MPa,30 秒)的 Li1Si 粒子的 FIB/SEM 橫截面圖像。c 不同壓力和時(shí)間下 Li1Si 的 7Li NMR 圖譜。
為了更好地了解 SLMP 和 μSi 前驅(qū)體加壓形成合金的程度,研究人員使用 7Li ssNMR 來探測塊狀鋰化硅的化學(xué)態(tài)。sNMR 在這里至關(guān)重要,因?yàn)殇嚮枋菬o定形的,無法使用標(biāo)準(zhǔn)衍射方法進(jìn)行研究。另一方面,7Li ssNMR 對結(jié)晶相和無定形相都很敏感,可以區(qū)分金屬鋰(265 ppm)和鋰硅合金(以 0 ppm 為中心的寬信號),并在理論上對其進(jìn)行量化,因?yàn)樗鼈兏髯缘男盘柖寄艿玫胶芎玫姆直?。然而,?ssNMR 測量中用于激發(fā)核自旋的射頻 (RF) 脈沖對金屬樣品的穿透力是有限的,并且與電子電導(dǎo)率的平方根成反比。這導(dǎo)致在選定的實(shí)驗(yàn)條件下,金屬鋰(電子電導(dǎo)率為 1.1 × 107 S/cm)的所謂 "表皮深度 "約為 7.4 μm,低于某些原始 SLMP 粒子的半徑(5-30 μm),因此會導(dǎo)致低估樣品中金屬鋰的含量。樣品中形成的鋰硅合金相的導(dǎo)電性比金屬鋰低很多個(gè)數(shù)量級,這將在下一節(jié)中討論,其最小表皮深度約為 570 μm(根據(jù) Li2Si 電子導(dǎo)電性計(jì)算得出),這確保了可以使用 7Li ssNMR 對這些區(qū)域進(jìn)行定量探測。不過,研究人員注意到,Li-Si 合金信號很可能與金屬 Li 表面不可避免形成的輕微二磁雜質(zhì)相重疊(即使通過始終在手套箱中處理樣品避免了空氣/水分暴露),包括共振頻率為 ~0 ppm 的 LiOH 和 Li2CO3。在圖 2c 中,對幾個(gè) SLMP + μSi 樣品進(jìn)行了 7Li ssNMR 測試,測試壓力從 0 到 400 MPa 不等,持續(xù)時(shí)間為 30 秒到 3 分鐘,以確定在什么條件下可以實(shí)現(xiàn)最大的硅預(yù)鋰化。
鑒于壓制樣品中金屬鋰子域的粒度分布與 SLMP 前驅(qū)體的粒度分布相同,盡管存在表皮深度問題,但 7Li ssNMR 檢測到的金屬鋰的相對數(shù)量與本研究關(guān)注的樣品中金屬鋰的實(shí)際數(shù)量呈相同趨勢。這樣,研究人員就可以利用 7Li ssNMR 圖譜中金屬鋰和鋰硅合金信號的相對綜合強(qiáng)度來跟蹤鋰在硅中的摻入情況與樣品加工條件的函數(shù)關(guān)系。數(shù)據(jù)采集過程中 ssNMR 信號(T2*)弛豫的影響已在所有樣品的可觀察到的鋰信號量化中考慮在內(nèi),但未壓制的 Li1Si 除外,由于樣品在圖譜儀中的演變,無法對其進(jìn)行 T2* 測量。未壓制的 Li1Si 樣品含有最多的金屬鋰和較小部分的鋰硅相,0 ppm 共振占 7Li ssNMR 信號強(qiáng)度總量的 27.8%。盡管沒有對該樣品進(jìn)行 T2* 調(diào)整,但由于其他樣品的鋰金屬或二磁性相經(jīng)過 T2* 調(diào)整后的鋰摩爾百分比變化小于 1%,因此這些結(jié)果預(yù)計(jì)是成立的。
相反,壓制的 Li1Si 樣品在 0 ppm 時(shí)的 7Li 信號強(qiáng)度大于總信號強(qiáng)度的 92%,表明存在主要的鋰硅合金相。與鋰金屬信號相比,0 ppm 信號的相對強(qiáng)度隨著壓力的增加和壓制時(shí)間的延長而增加,這表明樣品中的鋰硅合金比例增加。例如,與施加相同壓力 30 秒(藍(lán)色)相比,施加 200 MPa壓力 3 分鐘(綠色)會使更多的鋰摻入硅相中,這兩個(gè)樣品在 0 ppm 處的 7Li ssNMR 信號強(qiáng)度分別占總信號強(qiáng)度的 98.2% 和 92.9%。這些結(jié)果表明,在沒有電解質(zhì)的情況下,通過對 SLMP 和 μSi 前驅(qū)體粉末加壓可以形成鋰硅合金,這表明與之前的想法不同,促進(jìn)合金化反應(yīng)并不需要電解質(zhì)。有趣的是,未壓制的 LixSi 樣品在 ssNMR 測量過程中會發(fā)生變化,而壓制樣品的成分則保持穩(wěn)定。比較了在 T2* 弛豫時(shí)間測量之前、期間和之后對四個(gè)不同的 LixSi 樣品(Li1Si 和 Li2Si 未加壓和在 200 MPa加壓 30 秒)收集的 7Li ssNMR 圖譜。對于未加壓的樣品,0 ppm 信號在測量過程中不斷增加,表明鋰硅合金化正在隨著時(shí)間的推移而發(fā)生。另一方面,壓制樣品的圖譜不會發(fā)生變化,因?yàn)楣枰呀?jīng)在 200 MPa斯卡的壓力下被鋰化,并且在環(huán)境條件下保持穩(wěn)定。 對稱電池、半電池和全電池中 LixSi 的電化學(xué)比較
雖然硅是一種半導(dǎo)體,但其電子導(dǎo)電率較低(范圍在 10-4 S cm-1 之間),導(dǎo)致電池內(nèi)部存在較大的過電位。克服這一障礙的傳統(tǒng)方法是添加碳或一些導(dǎo)電劑,形成硅復(fù)合陽極。然而,在硅中添加鋰可能是大幅提高硅電子導(dǎo)電性的另一種方法。圖 3a 顯示,隨著鋰含量的增加,LixSi 的電子電導(dǎo)率從 10-4(Li0Si)增加到 10 S cm-1(Li2Si)。由于壓力誘導(dǎo)硅鋰化在上一節(jié)中被證明是一種有效的方法,研究人員評估了 LixSi 在對稱電池、半電池和全電池配置下的電化學(xué)特性。在圖 3b 中,研究人員對 LixSi 對稱電池進(jìn)行了沉積和剝離,以評估每個(gè)電池的過電位。電池的過電位隨著硅中鋰含量的增加而降低,這與圖 3a 中鋰離子含量較高的硅具有較高的電子導(dǎo)電性是一致的。高電子導(dǎo)電性的 Li2Si 對稱電池的過電位比 Li0.25Si 對稱電池小得多。利用電化學(xué)阻抗譜(EIS)分別評估了鋰硅對稱電池鍍鋰和脫鋰前后的電阻,見圖 3c、d。在沉積和剝離之前,Li0.25Si 的電阻高于 Li1Si 或 Li2Si(請注意,約 35 歐姆的電阻主要來自兩個(gè)電極之間 LPSCl 膠粒的離子導(dǎo)電性(約 2.2 mS cm-1)。沉積和剝離后電阻值略有下降,保持了硅中鋰含量越高阻抗越低的趨勢。沉積前后 Li1Si 和 Li2Si 的電阻值與硫化物電解質(zhì) Li6PS5Cl(LPSCl)電解質(zhì)層的離子導(dǎo)電率相當(dāng),表明 Li1Si 和 Li2Si 不是電池電阻的主要成分。圖 3e 顯示了含金屬鋰的 LixSi 的半電池結(jié)構(gòu)。在相同的電流密度下,所有 LixSi 首先鋰化 1 小時(shí),然后再脫鋰化 1 小時(shí)。
有趣的是,所有鋰硅在鋰化過程中都表現(xiàn)出相似的過電位,這表明鋰與硅反應(yīng)生成鋰硅需要相似的過電位。由于非新鋰化硅的電子傳導(dǎo)性較差,因此在首次鋰化時(shí)明顯表現(xiàn)出較高的過電位。然而,去鋰化過程的過電位卻因預(yù)鋰化程度的不同而明顯不同。這表明,預(yù)鋰化的程度最終會影響硅在充放電過程中的電子/離子導(dǎo)電性。在第一個(gè)周期中,不可逆容量有兩個(gè)來源:一個(gè)是界面上的電解質(zhì)分解,另一個(gè)是被困在 Si 中的鋰。
圖 3:對稱電池和半電池中 LixSi 的電導(dǎo)率和電化學(xué)性質(zhì)。
在圖 4a 中,制作了具有以下配置(LixSi | LPSCl | LCO)的全電池,并在 C/20 下進(jìn)行循環(huán),以研究硅中不同預(yù)鋰化量的影響,從而評估在鋰庫存有限的情況下的首次循環(huán)性能。雖然所有 LixSi 的充電容量相似,但其放電容量卻存在顯著差異。圖 3e 中的半電池配置也反映了這一結(jié)果,其中硅的鋰化(充電)效果相當(dāng),但硅的脫鋰(放電)則顯示出 ICE 的巨大變化。LCO-Si 全電池的 ICE 為 78.3%,而 LCO-Li1Si 和 LCO-Li2Si 的 ICE 則增加到 95% 以上(圖 4b)。
圖 4:LixSi 全電池的第一周期性能。a 不同鋰化狀態(tài)下 LixSi 全電池的第一周期電壓曲線。LCO | LPSCl | LixSi 電池在室溫和 75 MPa下循環(huán)。b LixSi 的初始庫侖效率趨勢(x = 0、0.25、1 和 2)。
陰極限制或陽極限制:NCM811/LCO 和 Si/Li1Si
兩種不同的陰極分別與 Si 和 Li1Si 配對,以闡明系統(tǒng)的極限成分(圖 5)。根據(jù)每種成分與鋰對電極的半電池?cái)?shù)據(jù),研究人員可以假設(shè) NCM 的 ICE 為 75%,Si 為 80%,LCO 為 95%。對于與硅和鋰化硅配對的 NCM 和 LCO 陰極,研究人員可以假設(shè)四種情況。(圖 5a)對于 NCM/Si 全電池,整體 ICE 受 NCM ICE 的限制,而 Si ICE 則決定了 LCO/Si 全電池的 ICE。因此,將 NCM 與陽極側(cè)有過量鋰的鋰化硅配對,電池仍將受到 NCM 的 ICE 限制,無法利用過量的鋰。然而,通過將 LCO 與鋰化硅配對,研究人員可以在第一次放電時(shí)利用過量的鋰,電池可以達(dá)到 LCO 的 ICE 限制,產(chǎn)生 95% 的電量。
因此,case 1(NCM/Si)和case 3(NCM/LixSi)可視為陰極限制系統(tǒng),而case 2(LCO/Si)則是陽極限制系統(tǒng)。這意味著只有當(dāng)全電池是陽極受限時(shí),預(yù)鋰化才會有效。為了證明這一假設(shè),研究人員分別制作了這四種情況下的電池。圖 5b 顯示的是 NCM811 的情況,預(yù)剝離后,C/20 時(shí)的 ICE 改善微乎其微。然而,LCO 電池的 ICE 從 78.3% 顯著提高到 95.7%(圖 5c)。這些電池的第一周期電壓曲線與圖 5a case 2 和case 4 中的假設(shè)一致。由于圖 5a case 4 實(shí)現(xiàn)了 95.7% 的最高 ICE,因此進(jìn)一步的長循環(huán)和更高的加載努力都是在這種配置下進(jìn)行的。
圖 5:預(yù)鋰化驅(qū)動(dòng)的陰極陽極極限情況改善。a Si 和 Li1Si 與 NCM 和 LCO 陰極配對的 ICE 估計(jì)值示意圖。在 C/20 條件下,(b) NCM811 和 (c) LCO 與 Si 和 Li1Si 配對的第一周期電壓曲線。
關(guān)于 N/P 比,還有一點(diǎn)很重要。雖然圖 5a 中的插圖解釋了全電池的 ICE 取決于基于 1 左右 N/P 比的陰極/陽極限制系統(tǒng),但研究人員在相對較高的 4.4 N/P 比下獲得了實(shí)驗(yàn)結(jié)果(圖 5b、c)。高 N/P 比通常會降低 ICE,因?yàn)椴豢赡娴腖i/電子消耗發(fā)生在相對較高的電壓下(鋰化過程的初始階段)。然而,研究人員的結(jié)果表明,N/P 比范圍較寬(1 ~ 3.3)的全電池表現(xiàn)出相似的 ICE 值,因?yàn)橐恍┱龢O部件實(shí)際上沒有參與鋰化過程。這使得研究人員的固態(tài)電池的有效 N/P 比約為 1,與圖示一致。因此,本節(jié)開頭關(guān)于情況 1 至情況 4 的討論即使在硅負(fù)載較高的情況下也是有效的。
預(yù)鋰化硅的斜坡測試和長周期循環(huán) 為了評估鋰化對臨界電流密度的影響,使用硅(圖 6a)和鋰一硅(圖 6b)進(jìn)行了斜坡測試。硅和 Li1Si 都沒有發(fā)生短路,即使電流達(dá)到 10 mA cm-2。所有電池中 LCO 陰極復(fù)合材料的等面積容量均為 4 mAh cm-2。在 0.25 mA cm-2 下的第一個(gè)循環(huán)中,兩種電池顯示出相似的充電容量,這表明陰極材料在相同負(fù)載下的利用率很高。然而,從第一個(gè)放電步驟開始,容量差異開始占據(jù)主導(dǎo)地位,與 Li1Si 電池配對時(shí),容量差異總是更大。圖 6c 顯示了硅電池和 Li1Si 電池在 5 mA cm-2 下的循環(huán)穩(wěn)定性。即使在 1.25 C(1 C = 4.0 mAh cm-2)的高速率下,鋰離子電池在 1000 次循環(huán)后的保持率也達(dá)到了 73.8%,平均 CE 為 99.9%,而非鋰化硅電池在 1000 次循環(huán)后的保持率為 58.7%。如圖 3e 所述,對于全硅電池而言,可逆容量的降低源于界面(尤其是 LPSCl/Si 界面)上的電解質(zhì)分解以及鋰被困在硅中。盡管在最初幾個(gè)循環(huán)后穩(wěn)定的 LPSCl/Si 界面有助于硅全電池獲得出色的可逆容量和可循環(huán)性,但可以清楚地看到,鋰存量較多(通過預(yù)鋰化產(chǎn)生過量鋰)的電池具有更好的可循環(huán)性。這進(jìn)一步證明了室溫鋰化硅電池可以在長時(shí)間循環(huán)中以較高的速率工作。
圖 6:硅電池和 Li1Si 全電池的循環(huán)性能。評估 (a) 硅電池和 (b) 硅鋰電池臨界電流密度的斜坡測試。c 硅電池和鋰離子電池在 5 mA cm-2 下的循環(huán)性能。有趣的是,鋰化硅的循環(huán)趨勢顯示出初始放電容量增加而不是衰減。為了更好地了解全電池,對兩種情況下的循環(huán)進(jìn)行了 EIS 測量。這種初始放電容量的增加可能是由于未鋰化為 LixSi 的殘余鋰金屬在隨后的循環(huán)中發(fā)生了電化學(xué)鋰化。
考慮到電池中使用的硅量,所有電池都顯示出較高的 N/P 比。所有電池的硅用量固定為 5 mg,理論陽極容量約為 14 mA時(shí),N/P 約為 4.4。因此,需要增加陰極負(fù)載以匹配陽極的高容量。然而,關(guān)于高負(fù)載厚電極,之前有報(bào)道稱厚電極內(nèi)部存在不均勻反應(yīng),顯示出鋰離子擴(kuò)散限制,導(dǎo)致電荷狀態(tài)變化。因此,為了在厚電極內(nèi)實(shí)現(xiàn)更均勻的電化學(xué)途徑,研究人員制作了一種由陰極、陰極溶液和聚四氟乙烯(PTFE)粘結(jié)劑組成的干法陰極薄膜。高負(fù)載 10.8 mAh cm-2 電池的能量密度計(jì)算結(jié)果為 236 Wh kg-1 和 947 Wh L-1(假設(shè)固體電解質(zhì)層為 30 μm)。
全固態(tài)硅電池已顯示出巨大的潛力,可實(shí)現(xiàn)高容量陽極而無需持續(xù)的 SEI 生長。然而,硅的低ICE仍然是全固態(tài)電池需要克服的一個(gè)挑戰(zhàn)。在此,研究人員采用了一種使用穩(wěn)定鋰的預(yù)鋰化策略,以提高陽極的內(nèi)切效率和導(dǎo)電性。在對稱、半電池和全電池配置中對鋰化硅進(jìn)行了研究,以了解每種成分在電池級的改進(jìn)情況。在將 Li1Si 和 LCO 分別用作陽極和陰極的情況下,全電池顯示出超過 95% 的 ICE。在這項(xiàng)工作中,研究人員通過比較 NCM 和 LCO 與 Si 和 LixSi 的搭配,找出了預(yù)鋰化效應(yīng)僅在陽極受限情況下占主導(dǎo)地位的原因。研究人員對 Si 和 Li1Si 電池的斜坡測試和長循環(huán)性能進(jìn)行了評估。經(jīng)過 1000 次循環(huán)后,鋰離子電池的性能大幅提高了 73.8%,保持率提高了 15%。此外,使用 Li1Si,干法 LCO 薄膜實(shí)現(xiàn)并展示了 10 mAh cm-2 的高等效容量,這表明鋰化硅可能是下一代高能量密度電池的合適候選材料。
-
鋰離子電池
+關(guān)注
關(guān)注
85文章
3255瀏覽量
77943 -
電解質(zhì)
+關(guān)注
關(guān)注
6文章
820瀏覽量
20167 -
EDS
+關(guān)注
關(guān)注
0文章
96瀏覽量
11594 -
全固態(tài)電池
+關(guān)注
關(guān)注
0文章
57瀏覽量
4880 -
硅電池
+關(guān)注
關(guān)注
0文章
9瀏覽量
2118
原文標(biāo)題:孟穎(Y. Shirley Meng)教授最新Nature子刊:全固態(tài)電池中預(yù)鋰化!
文章出處:【微信號:清新電源,微信公眾號:清新電源】歡迎添加關(guān)注!文章轉(zhuǎn)載請注明出處。
發(fā)布評論請先 登錄
相關(guān)推薦
?什么是水質(zhì)電導(dǎo)率變送器?
全固態(tài)鋰金屬電池的最新研究
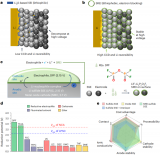
王東海最新Nature Materials:全固態(tài)鋰硫電池新突破
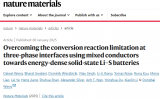
電導(dǎo)率單位在工業(yè)應(yīng)用中的作用
電導(dǎo)率單位在環(huán)境監(jiān)測中的使用
電導(dǎo)率的定義和測量原理
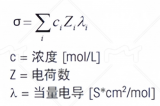
全固態(tài)鋰金屬電池的鋰陽極夾層設(shè)計(jì)
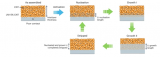
電導(dǎo)率測定儀的基礎(chǔ)應(yīng)用與探索
純鋰新能源全固態(tài)電池成功量產(chǎn)
電導(dǎo)率測定儀的應(yīng)用優(yōu)勢
高能數(shù)造鋰金屬全固態(tài)電池小試級整線正式交付
電導(dǎo)率的檢測方法有哪幾種
測電導(dǎo)率需要注意哪些事項(xiàng)
眾多企業(yè)發(fā)布固態(tài)電池的布局動(dòng)態(tài)
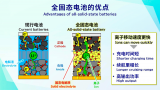
7芯M9接頭的電導(dǎo)率高嗎

評論