文章來源:學習那點事
原文作者:趙先生
本文主要介紹銅大馬士革工藝
概述
銅相較于鋁,展現(xiàn)出較低的電阻率(銅為1.67微歐·厘米,鋁為2.67微歐·厘米)和更強的電遷移抗力(銅的晶格與晶界擴散能分別為2.2eV和0.7至1.2eV,而鋁則分別為1.4eV和0.4至0.8eV),賦予了它更高的可靠性。銅也有顯著的短板:首要的是粘附力弱,難以緊密貼合硅基板,易于剝離;其次,銅易滲透至硅及其化合物中,可能引發(fā)集成電路失效;再者,銅在空氣中易于氧化,且形成的氧化層不夠緊密,無法有效防止進一步氧化;最后,缺乏高效的銅刻蝕手段。所以在較長一段時間內(nèi),鋁及其合金因能滿足集成電路互聯(lián)需求而得以廣泛應用。
但隨著技術迭代,晶體管尺寸持續(xù)縮減,電阻電容(RC)延遲已成為制約集成電路性能的關鍵因素。在90納米及以下工藝節(jié)點,銅開始作為金屬互聯(lián)材料取代鋁,同時采用低介電常數(shù)材料作為介質(zhì)層,這一轉(zhuǎn)變主要依賴于銅大馬士革工藝(包括單鑲嵌與雙鑲嵌)與化學機械拋光(CMP)技術的結(jié)合。
大馬士革鑲嵌工藝原指將貴金屬嵌入其他金屬中制作藝術品,銅互聯(lián)線則借鑒此理念,先在介質(zhì)層上刻蝕出溝槽和孔洞,再填充銅,隨后通過CMP技術去除多余的銅,形成所需電路圖案,從而繞開了銅刻蝕難題。與傳統(tǒng)鋁互聯(lián)工藝相比,銅互聯(lián)工藝有望減少20%至30%的步驟,簡化流程,降低成本,減少生產(chǎn)錯誤,對大規(guī)模芯片生產(chǎn)極為有利。
在當前的后端工藝中,第一層金屬層M1主要采用單鑲嵌工藝,而M2至Mx層因涉及通孔層與金屬層,故多采用雙鑲嵌工藝,即同時形成兩層結(jié)構(gòu)。雙鑲嵌工藝又可細分為先通孔、先溝槽和自對準三種類型。
單鑲嵌工藝
以下以M1金屬層沉積為例,簡述單鑲嵌工藝。整個M1工藝流程可詳細劃分為薄膜沉積、圖案曝光與顯影、介質(zhì)層蝕刻、阻擋層構(gòu)建、種子層沉積、銅電鍍以及化學機械拋光等多個關鍵環(huán)節(jié)。本文將逐一深入解析每個步驟的具體內(nèi)容。
(1)如圖1所示,首先在接觸孔上方,利用等離子體增強化學氣相沉積(PECVD)技術,依次沉積了氮摻雜碳化硅(NDC,即SiCN)層、金屬間介質(zhì)(IMD)層以及四乙氧基硅烷(又稱正硅酸乙酯,TEOS)層。其中,NDC層作為蝕刻阻擋層,不僅充當介質(zhì)層蝕刻的終止層,還能有效阻止銅原子的擴散;IMD層則采用了低介電常數(shù)(low-k)材料,作為金屬線之間的絕緣介質(zhì);而TEOS層則作為黏附層,覆蓋在低介電常數(shù)的硅氮烷聚合物(如Black Diamond,BD)之上,增強了底部抗反射涂層(BARC)與BD層之間的黏附力,避免了薄膜剝落的風險。
圖1:沉積薄膜層
(2)如圖2所示,旋涂BARC和光刻膠(PR),并進行曝光顯影。
圖2:旋涂BARC和光刻膠(PR)
(3)進行M1層的蝕刻。如圖3所示,通過一步蝕刻工藝,同時穿透TEOS/BD/NDC層,形成了M1溝槽。這一過程中,需要確保蝕刻穿透阻擋層,使接觸孔(CT)中的鎢(W)暴露出來,以便與后續(xù)的M1層實現(xiàn)電氣連接。在此過程中,有幾個關鍵參數(shù)需要特別注意,包括層間介質(zhì)(ILD)的損失量、氮化鈦(TiN)的殘留量以及側(cè)壁的角度。
圖3:M1刻蝕
(4)沉積金屬阻擋層TaN/Ta,如圖4所示。這一步驟的目的是為了阻止銅原子向介質(zhì)層中的擴散,同時提供良好的電接觸和機械支撐。
圖4:沉積金屬阻擋層
(5)進行銅金屬互連層的沉積。這一過程主要分為三個步驟:首先是銅種子層的生長,為后續(xù)的銅電鍍提供必要的導電基礎;接著是銅的電化學鍍膜(ECP)工藝處理,通過電化學方法將銅沉積在種子層上,形成所需的銅互連線;最后是銅的化學機械拋光(CMP)工藝處理,通過機械和化學的雙重作用,去除晶圓表面多余的銅材料,得到平整、精確的銅互連圖案,如圖5所示。
圖5:沉積銅金屬互連層
雙鑲嵌工藝-先通孔(via first)
在雙鑲嵌工藝體系中,先通孔技術遵循的是先形成通孔,隨后開辟金屬溝槽的順序。以M2金屬層的制作為例,該技術的核心步驟涵蓋薄膜沉積、通孔的光刻與刻蝕、金屬溝槽的光刻與刻蝕、阻擋層的沉積、種子層的沉積、銅的電鍍以及化學機械拋光等。(1)如圖6所示,依次沉積NDC、TEOS、IMD、TEOS層。
圖6:薄膜沉積
(2)接著進行通孔的光刻步驟,如圖7所示。此環(huán)節(jié)涉及底部抗反射涂層(BARC)和光刻膠(PR)的旋涂,以及后續(xù)的曝光與顯影處理。
圖7:通孔的光刻處理
(3)進行通孔的刻蝕,直至抵達NDC層,并保留一定厚度的NDC作為刻蝕停止層,如圖8所示。
圖8:刻蝕通孔
(4)在填充BARC后,我們沉積了低溫氧化硅(LTO)層,該層作為后續(xù)蝕刻的硬掩模,如圖9所示。然而,由于BARC的填充,后續(xù)溝槽蝕刻過程中通孔內(nèi)可能殘留BARC,這是先通孔技術的一個固有缺陷。
圖9:刻蝕填充
(5)進行溝槽部分的曝光顯影,如圖10所示。
圖10:溝槽曝光顯影
(6)進入溝槽刻蝕階段,如圖11所示。此過程需先形成溝槽,再清除通孔內(nèi)的BARC殘留。溝槽的深度需通過精細調(diào)整蝕刻工藝配方來控制,對蝕刻工藝提出了更高要求。為了實現(xiàn)更精準的深度控制,可在BD層中嵌入如氮化硅(SiN)層等蝕刻阻擋層,以限制溝槽蝕刻深度,防止過蝕刻導致的深度失控。但需注意,增加阻擋層可能會提升IMD層的整體介電常數(shù)(k值),因此需根據(jù)實際需求進行權(quán)衡。
圖11:溝槽刻蝕
(7)最后進行阻擋層與銅的沉積,并實施銅的化學機械拋光(CMP)處理,如圖12和圖13所示。這些步驟的基本方法與之前M1層中的操作相似,故不再贅述。對于M3至Mx層,同樣采用此方法。
圖12:沉積阻擋層
圖13:沉積銅和銅CMP處理
在55納米工藝節(jié)點,先通孔技術雖占據(jù)主導地位,但其存在的缺陷不容忽視:一是通孔內(nèi)BARC的完全去除較為困難,易導致殘留;二是溝槽尺寸存在擴張現(xiàn)象(見圖14),可能引發(fā)互連線間的橋接短路風險,從而無法滿足更先進工藝節(jié)點的要求。
圖14:先通孔造成溝槽擴張
雙鑲嵌工藝-先溝槽(trench first)
在雙鑲嵌工藝體系中,先溝槽技術遵循的是先形成溝槽結(jié)構(gòu),隨后開辟通孔的步驟。該技術的核心流程包括薄膜沉積、溝槽的光刻與蝕刻、通孔的光刻與蝕刻、阻擋層的沉積、種子層的鋪設、銅的電鍍以及化學機械拋光等關鍵環(huán)節(jié)。
(1)依次沉積NDC,IMD,TEOS,TiN,SiO2層,如圖15所示。其中,TiN層扮演著金屬硬掩模的角色,旨在優(yōu)化光刻與刻蝕的工藝分辨率,從而更精確地控制溝槽與通孔的圖形尺寸,提升光刻線條的精度。但是在蝕刻完成后,TiN層需被去除。最頂層的SiO2層則主要起到隔離光刻膠(PR)層與金屬硬掩模層的作用,防止它們直接接觸,并具備良好的黏附性能。
圖15:薄膜沉積
(2)對溝槽進行光刻處理,并通過硬掩??涛g將光刻膠上的圖形轉(zhuǎn)移到硬掩模上。隨后,原位灰化并剝離上層剩余的PR和底部抗反射涂層(BARC),如圖16所示。
圖16:溝槽光刻和掩膜層刻蝕
(3)進入溝槽蝕刻階段,通過金屬掩模版開口向下蝕刻介電層,形成溝槽結(jié)構(gòu),如圖17所示。為了更精確地控制蝕刻深度,可以在介電層中嵌入一層刻蝕阻擋層(如SiN等)。
圖17:溝槽刻蝕
(4)填充PR和BARC,并進行通孔的光刻處理,如圖18所示。
圖18:通孔光刻
(5)通過通孔刻蝕并去除PR和BARC,得到包含溝槽與通孔的結(jié)構(gòu),如圖19所示。
圖19:通孔刻蝕
(6)最后進行金屬沉積(包括阻擋層與銅的沉積),并實施化學機械拋光(CMP)處理,如圖20所示。
圖20:金屬沉積及CMP處理
先溝槽技術的一個顯著優(yōu)勢在于它避免了溝槽擴張現(xiàn)象,因此可以在更先進的工藝節(jié)點中使用。然而,在通孔光刻過程中,PR會填充到溝槽中,導致PR層變厚,從而增加了曝光與顯影的難度。為了進一步優(yōu)化先溝槽工藝,探索出一步蝕刻技術,即同時形成溝槽與通孔。這一改進有助于解決PR填充帶來的問題,并提升蝕刻效果。具體步驟如下:
①沉積NDC,IMD,TEOS,TiN,SiO2層。
②對溝槽進行光刻處理,并通過硬掩模蝕刻將光刻膠上的圖形轉(zhuǎn)移到硬掩模上。隨后,原位灰化并剝離上層剩余的PR和BARC。
③進行通孔的光刻處理:在不進行溝槽蝕刻的情況下,再次進行曝光與顯影,形成通孔的圖形,如圖21所示。
圖21:通孔光刻
④采用一步蝕刻技術同時形成溝槽與通孔結(jié)構(gòu)。首先部分蝕刻出通孔圖形,去除PR和BARC后,繼續(xù)蝕刻以形成完整的溝槽與通孔結(jié)構(gòu),如圖22所示。
⑤最后進行金屬沉積(包括阻擋層與銅的沉積),并實施CMP處理。
雙鑲嵌工藝-自對準(self-aligned)
在雙鑲嵌工藝的范疇內(nèi),存在一種能夠同步刻蝕以形成溝槽與通孔的先進方法,即所謂的自對準技術。以下是該技術的具體工藝流程概述:(1)依次沉積NDC(氮化硅或氮氧化硅等介質(zhì)材料)/BD(底層介質(zhì),如二氧化硅)/SiN(氮化硅,作為刻蝕阻擋層,其他材料如NDC亦可選用)層,如圖23所示。
圖23:薄膜沉積
(2)對阻擋層進行光刻與蝕刻處理,以形成與通孔尺寸相匹配的圖案,如圖24所示。
圖24:阻擋層刻蝕
(3)接著再次沉積BD/TEOS(四乙基正硅酸酯,一種常用的介質(zhì)材料)/TiN(氮化鈦,常用于硬掩模或擴散阻擋層)/SiO2層,如圖25所示。
圖25:薄膜沉積
(4)進入溝槽光刻階段,如圖26所示,通過光刻技術定義出溝槽的圖形。
圖26:溝槽光刻
(5)最后實施一步刻蝕工藝,同時形成溝槽與通孔。此過程中,刻蝕首先向下進行以形成溝槽結(jié)構(gòu),當?shù)竭_刻蝕阻擋層時,刻蝕工藝繼續(xù),穿透阻擋層以形成通孔結(jié)構(gòu)。這樣,通過一次刻蝕步驟即完成了溝槽與通孔的形成。后續(xù)的阻擋層沉積、金屬沉積等步驟則與雙鑲嵌工藝中的先溝槽技術保持一致。
銅阻擋層、種子層及電鍍銅
在銅互連工藝中,阻擋層扮演著至關重要的雙重角色:一是防止銅原子滲透至下方的介電層(例如SiCOH)中,以免破壞絕緣性能;二是確保銅層能夠牢固地黏附于基底之上。鑒于銅的高度活性及其易于在介電材料中擴散的特性,特別是在采用低介電常數(shù)或超低介電常數(shù)材料時,銅擴散問題尤為嚴峻,傳統(tǒng)的阻擋材料(諸如Ti、TiN)已難以勝任。因此,阻擋層的設計需兼顧高熱穩(wěn)定性、與銅及介電層的良好黏附性、出色的保形性和臺階覆蓋能力,以及與銅化學機械拋光(CMP)工藝的兼容性。
當前,TaN/Ta組合已成為銅阻擋層的首選材料,因其對銅的擴散激活能極高,能有效遏制銅的擴散。TaN薄膜,特別是非晶態(tài),展現(xiàn)出卓越的防銅擴散能力,而增加TaN在金屬互連層中的比例可進一步提升可靠性。但是TaN與銅的黏附性欠佳,可能影響后續(xù)銅種子層的均勻沉積,故Ta層被用作黏附層,以促進大晶粒銅籽晶層的形成。注意作為金屬阻擋層,其通孔電阻亦需考量,但阻擋層材料往往具有較高的電阻率,對通孔電阻有顯著影響。因此,在確保阻擋性能的前提下,合理控制阻擋層厚度至關重要。
阻擋層的制備多采用物理氣相沉積(PVD)技術,但傳統(tǒng)濺射工藝的保形性不足,故離子化PVD工藝應運而生,隨后又開發(fā)了自離化等離子體(SIP)PVD系統(tǒng),進一步優(yōu)化了沉積工藝。SIP中,單純提升離子化濃度會導致底部沉積過多而側(cè)壁沉積不足。為解決這一問題,反濺射技術被引入,利用氬離子在襯底偏壓作用下濺射刻蝕,將底部多余的阻擋層材料反濺射至側(cè)壁,實現(xiàn)沉積厚度的重新分布,既減薄了底部沉積,又增厚了側(cè)壁沉積,從而改善了阻擋層的均勻性并降低了接觸電阻。
隨著器件尺寸的不斷縮小,原子層沉積(ALD)技術也開始應用于阻擋層的沉積。ALD以其卓越的保形性和填洞能力著稱,能夠?qū)崿F(xiàn)側(cè)壁的完美覆蓋,并能形成極?。s10?)且連續(xù)性好的薄膜,有助于增大銅線的有效截面積并降低電阻。然而,ALD亦面臨挑戰(zhàn),如與種子層間的黏附性問題以及沉積過程中氣體向多孔介質(zhì)材料中的擴散等,這些問題有待進一步研究與解決。
具體的沉積流程如圖27所示,首先進行TaN的沉積,然后進行Ta的沉積。接著,執(zhí)行刻蝕步驟以穿透位于溝槽底部的阻擋層薄膜,并緊接著快速沉積一層薄薄的金屬Ta。此快速鍍Ta步驟的核心目的在于保護雙大馬士革工藝的邊角完整性,特別是針對那些在刻蝕過程中可能遭受侵蝕而變薄的區(qū)域,從而增強工藝的整體可靠性與器件的穩(wěn)定性。TaN/Ta的沉積作業(yè)通常是在同一設備中完成,且普遍采用磁控濺射技術。沉積步驟概述如下:利用直流電源濺射Ta,同時應用交流偏壓以確保良好的覆蓋率,并將腔體設定為沉積模式,以提升沉積的均勻性。
圖27:阻擋層和銅沉積工藝
至于刻蝕步驟,則涉及降低直流功率以減少Ta的濺射量,防止線圈上的Ta因二次濺射而污染靶材。此時,交流偏壓被用來驅(qū)動Ar離子對晶圓上已沉積的Ta進行刻蝕/濺射,而直流線圈則持續(xù)提供Ta源,以避免通孔和溝道的邊角被過度刻蝕。射頻在低直流功率條件下維持等離子體的穩(wěn)定,同時腔體被設置為清潔模式,以防止靶材邊緣的Ta發(fā)生二次沉積。
如圖28所示,當前正致力于研發(fā)銅的直接電鍍技術,即省略銅種子層的沉積步驟,直接在阻擋層上進行銅的電鍍。這一技術革新對阻擋層提出了更高要求,包括更低的電阻率和更強的抗氧化能力。遺憾的是,即便是目前廣泛使用的Ta也難以完全滿足這些條件。釘(Ru)因其對銅具有更優(yōu)異的黏附性,被視為實現(xiàn)直接電鍍的潛在候選材料。然而,Ru在阻擋銅原子擴散方面的表現(xiàn)并不理想,因此可以考慮與TaN結(jié)合形成雙層結(jié)構(gòu)。不過Ru在化學機械拋光(CMP)過程中存在挑戰(zhàn),如在酸性條件下拋光會產(chǎn)生有毒的RuO氣體,而在堿性條件下拋光速率較慢,且易于形成缺陷,從而影響器件的可靠性。
圖28:電鍍銅工藝示意圖
除了雙層阻擋層的研究,單層阻擋層同樣也很重要。制備雙層薄阻擋層不僅工藝復雜,而且成本高昂。單層阻擋層的研究主要聚焦于合金薄膜,如RuTa合金、CoTi合金等。這些合金薄膜能夠同時滿足黏附和阻擋的雙重需求,為銅的直接電鍍提供了新的可能。
種子層與阻擋層的沉積過程頗為相似,常采用SIP濺射工藝或ALD工藝,以確保出色的臺階覆蓋能力。一個形狀保持完好、均勻且電阻率低的薄銅種子層,是電鍍銅工藝中實現(xiàn)溝槽無縫填充的關鍵前提。其厚度需控制在500至2000埃之間,過厚的種子層會減小開口尺寸,增大電鍍銅的難度,可能導致封口現(xiàn)象,從而在內(nèi)部遺留空洞。相反,若種子層過薄,側(cè)壁覆蓋不足,載流性能將大打折扣,電鍍過程中易形成缺陷,影響互連線的穩(wěn)定性。種子層的主要功能是提供成核點,促進大量銅晶粒和薄膜的形成,確保后續(xù)ECP(電鍍銅)的正常沉積及其均勻性。相較于其他金屬陽極(如Ti、Ta),銅更易于離化,自離化的等離子體狀態(tài)最為穩(wěn)定,且離化率最高。在銅的沉積過程中,還需特別注意防止銅的團聚,因為不連續(xù)的銅薄膜會顯著降低電鍍時的載流性能,因此,晶圓底座需具備良好的散熱性能。此外,在濺射工藝中,反濺射方法也被廣泛應用,以增強種子層在側(cè)壁的覆蓋。
ECP工藝在銅大馬士革工藝中占據(jù)著舉足輕重的地位。其基本原理是:將已完成阻擋層和銅種子層沉積的硅片晶圓正面朝下置于硫酸銅溶液中,晶圓背面通過金屬環(huán)與電源負極相連作為陰極,而銅塊則作為陽極預先置于鍍液中,以產(chǎn)生電鍍所需的銅離子。在直流電源的作用下,溶液中的銅離子向陰極移動,并在硅片表面形成銅膜。電鍍過程能夠?qū)崿F(xiàn)完美的填充效果。但是由于阻擋層和銅種子層本身存在一定的工藝瑕疵,如懸垂效應,因此在填充過程中可能會產(chǎn)生孔洞
為了消除電鍍銅過程中產(chǎn)生的孔洞,硫酸銅溶液會添加氯離子、氫離子及多種有機添加劑,這些添加劑通常包括加速劑、抑制劑和平整劑,它們協(xié)同作用以改善電鍍的均勻性和填充效果,并調(diào)控銅的晶粒大小。氫離子作為溶液中的電荷載體,能提升溶液的離子導電性,穩(wěn)定電鍍過程中的電場。氯離子則傾向于吸附在陽極和陰極表面,促進陽極銅的溶解,并在陰極捕捉銅離子,加速電子傳遞
加速劑,多為小分子有機高分子化合物,易于滲透至溝槽深處,提升銅的填充效率。其中,3-巰基-1-丙烷磺酸鈉(MPS)和聚二硫二丙烷磺酸鈉(SPS)是常用的加速劑,它們能與溝槽表面及底部的二價銅離子反應,生成一價銅離子,加速銅的還原沉積,實現(xiàn)溝槽的保形生長,此過程依賴氯離子的存在。
抑制劑和平整劑則具有較大的分子量,能抑制銅膜的生長。抑制劑主要防止電鍍時過早封閉開口,增強電鍍填充能力;平整劑則能減少因表面微觀結(jié)構(gòu)不均導致的過度電鍍,即抑制表面凸起的生長,簡化后續(xù)的化學機械拋光步驟。聚乙二醇(PEG)、聚丙二醇(PPG)或其共聚物常用作抑制劑,它們與銅、氯離子形成絡合物,阻礙銅表面的電荷交換。健那綠(JGB)是一種常用的平整劑,作為季銨鹽帶正電荷,傾向于吸附于高電荷密度區(qū)域如陰極尖端,實現(xiàn)平整效果,盡管其具體機制尚不完全清晰。
電鍍銅工藝與低k介質(zhì)具有良好的工藝兼容性,通常形成(111)方向的織構(gòu),有利于提升電導率。此外,電鍍銅具有“自退火”效應,能促進大銅晶粒的形成,降低材料電阻率。相較于小晶粒,大晶粒不僅提高了研磨速率20%以上,還減少了薄膜中的晶界數(shù)量,顯著增強了銅線的電遷移可靠性。
PVD法制備的銅種子層在生長時會延伸到硅片晶圓的邊緣甚至背面,這可能對后續(xù)工藝設備造成污染。邊緣區(qū)域的銅種子層表面均勻性不佳,會影響電鍍銅的形成,并可能導致薄膜脫落。因此,ECP后通常需進行邊緣去除(Edge Bevel Removal, EBR)處理。此過程包括:將鍍銅硅片正面朝上置于卡槽內(nèi)高速旋轉(zhuǎn),同時從硅片邊緣的噴嘴噴出一定比例的雙氧水和硫酸混合溶液,以去除硅片邊緣的銅層,而阻擋層則保留在硅片上。電鍍銅通過“自退火”效應形成較大的銅晶粒,但通常還需額外退火處理以進一步增大晶粒尺寸。在適宜條件下退火后,薄膜電阻率可降低約20%,晶粒大小可達1微米以上。但是退火也會帶來一些問題,如晶粒增大導致銅的張應力急劇增加(達300MPa),引起晶圓變形,影響后續(xù)工藝如CMP和光刻。并且退火過強可能增加銅線中的微缺陷,這些缺陷可能遷移聚集形成大孔洞,導致線路失效。使用特定添加劑雜質(zhì)可阻擋微缺陷遷移,提高銅線的應力遷移性能,但雜質(zhì)增多會降低銅線的電子遷移性能。因此,退火工藝的優(yōu)化是ECP中的關鍵環(huán)節(jié)。
完成ECP工藝后,需進行銅的化學機械拋光(CMP)工藝。CMP工藝首先以較高速率去除晶圓表面阻擋層以上的大部分銅,然后以較低速率去除殘余銅和阻擋層,最終實現(xiàn)表面平整化。銅研磨工藝常采用雙氧水作為氧化劑,使銅在溶液中氧化形成一價和二價銅離子。在酸性條件下可獲得較高的研磨速率,而在近中性或堿性溶液中研磨速率較低,需加入絡合劑形成可溶絡合物以提高研磨速率。SiO2是常用的磨料,其粒徑小且在不同條件下具有良好的懸浮性,研磨后可獲得良好的表面狀態(tài)。在去除殘留銅的過程中易發(fā)生過研磨,所以阻擋層研磨要求研磨液具有更好的速率選擇性,即阻擋層的研磨速率應大于銅的研磨速率。這通常通過使用兩種研磨液來實現(xiàn),以修正殘余銅研磨過程中產(chǎn)生的蝶形坑和蝕坑等缺陷。而且由于low-k材料的機械強度較低,阻擋層研磨時需采用更小的應力,以防止low-k介質(zhì)層變形或剝落,并盡量減少對介質(zhì)層結(jié)構(gòu)和性質(zhì)的破壞,以免影響其k值。
-
工藝
+關注
關注
4文章
605瀏覽量
28907 -
晶體管
+關注
關注
77文章
9764瀏覽量
138942 -
蝕刻
+關注
關注
9文章
420瀏覽量
15514
原文標題:銅大馬士革工藝
文章出處:【微信號:bdtdsj,微信公眾號:中科院半導體所】歡迎添加關注!文章轉(zhuǎn)載請注明出處。
發(fā)布評論請先 登錄
相關推薦
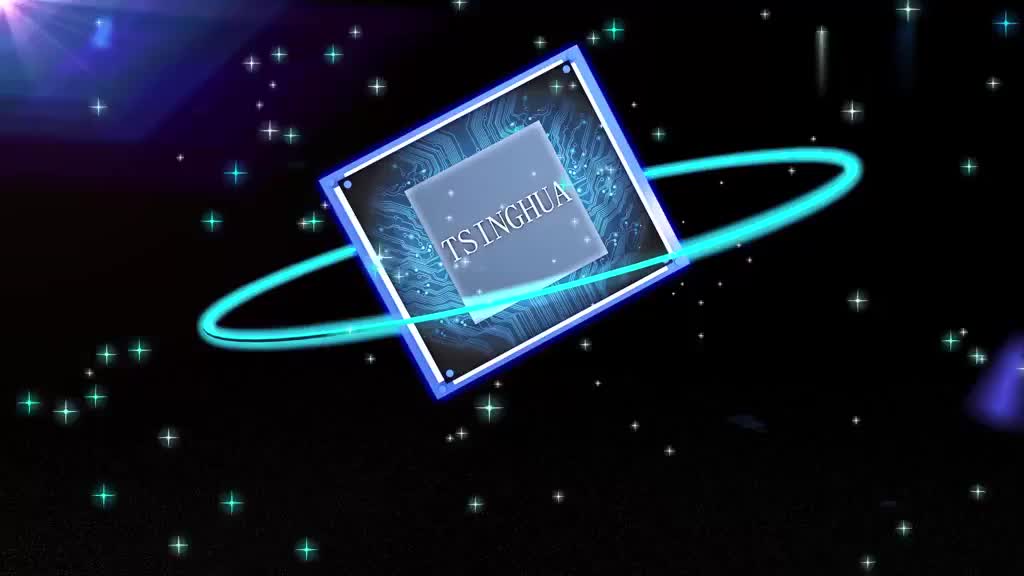
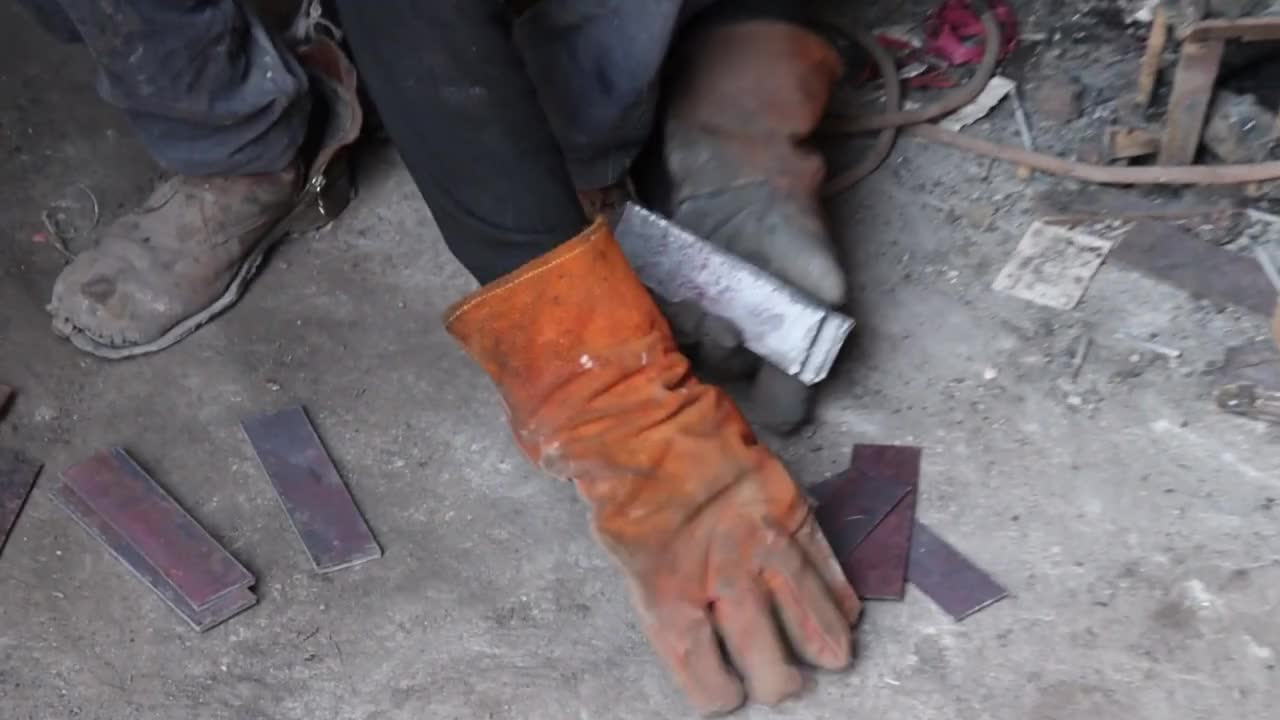
鐵匠鋪鍛打大馬士革花紋鋼酸洗之后花紋確實夠漂亮鍛打?鐵匠?大馬士革? #硬聲創(chuàng)作季
如何采用銅互連單大馬士革工藝制作超厚金屬銅集成電感的概述
12吋晶圓集成電路芯片制程工藝與工序后端BEOL的詳細資料說明
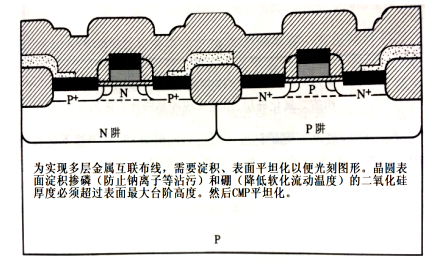
實現(xiàn)3nm技術節(jié)點需要突破哪些半導體關鍵技術
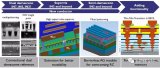
華進半導體專利再次獲評優(yōu)秀獎
半大馬士革集成中引入空氣間隙結(jié)構(gòu)面臨的挑戰(zhàn)
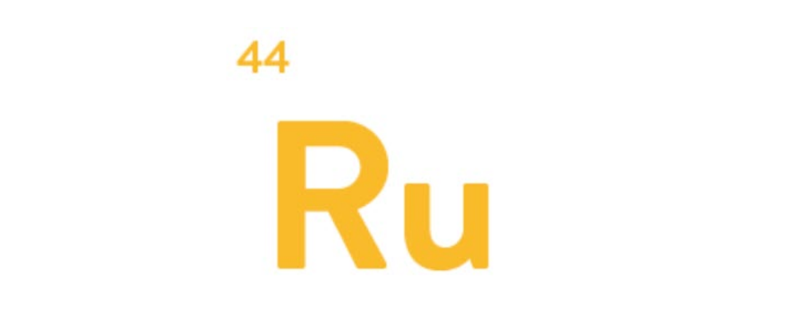
通過工藝建模進行后段制程金屬方案分析
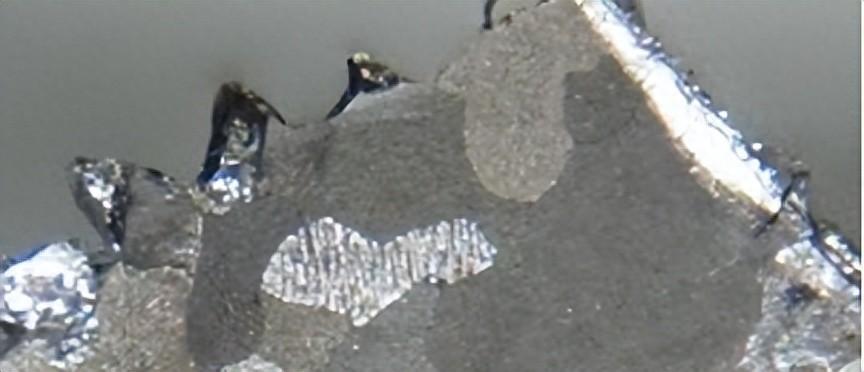
降低半導體金屬線電阻的沉積和刻蝕技術
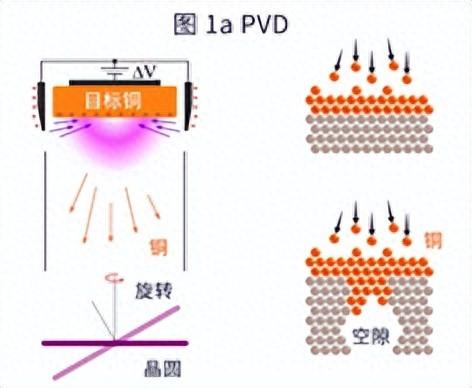
半大馬士革工藝:利用空氣隙減少寄生電容
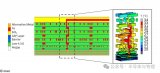
大馬士革銅互連工藝詳解
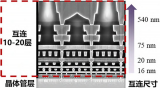
評論